Les disques abrasifs jouent un rôle essentiel dans de nombreux secteurs, facilitant le façonnage et la finition des matériaux. Cependant, comme tout autre outil, ils ne sont pas à l'abri de problèmes pouvant nuire à leur efficacité et à leurs performances. Dans cet article, nous examinerons les problèmes courants liés aux disques abrasifs, en explorerons les causes profondes et proposerons des solutions efficaces pour un flux de travail fluide.
Introduction
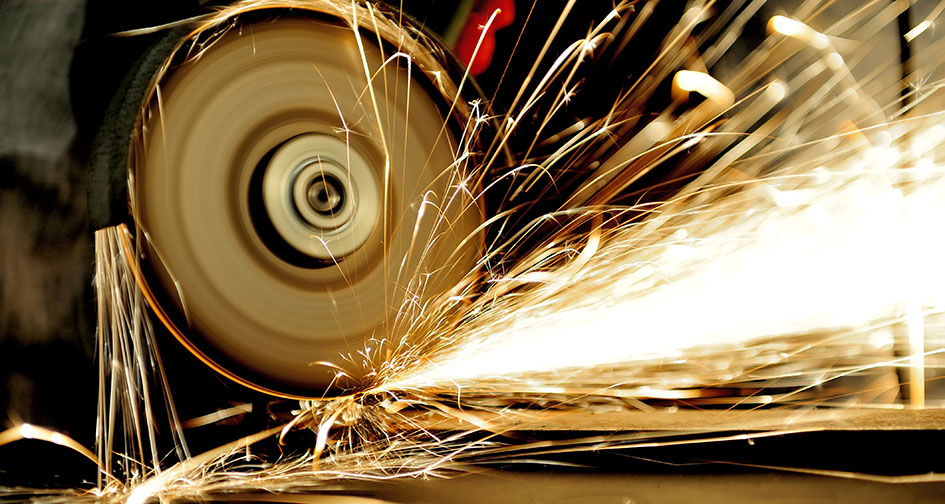
Les disques abrasifs jouent un rôle fondamental dans de nombreux secteurs industriels, constituant des outils essentiels pour l'enlèvement de matière, le façonnage et la finition. Comprendre leur définition, leur importance dans les différents secteurs et les problématiques courantes rencontrées est essentiel pour optimiser leur utilisation et garantir l'efficacité de leurs opérations.
A. Définition des disques abrasifs
Les disques abrasifs sont des outils utilisés dans les processus d'usinage pour couper, meuler ou polir les surfaces des matériaux. Ces disques sont généralement constitués de particules abrasives liées à un support, créant ainsi un outil rotatif capable d'éliminer l'excès de matière, de lisser les surfaces ou d'affûter les arêtes. Ils existent en différentes formes et tailles, chacune étant conçue pour des applications spécifiques.
B. Importance dans diverses industries
Industrie métallurgique :
Dans la fabrication et la transformation des métaux, les disques abrasifs sont essentiels pour le façonnage, l'ébavurage et la finition des surfaces métalliques. Ils sont couramment utilisés avec les meuleuses d'angle pour obtenir des dimensions précises et une qualité de surface optimale.
Industrie de la construction :
Les professionnels de la construction comptent sur les disques de meulage pour des tâches telles que la préparation de la surface du béton, le lissage des bords rugueux et l'élimination des imperfections dans des matériaux comme la pierre et le béton.
Industrie automobile :
Les disques abrasifs sont essentiels dans le secteur automobile pour des tâches allant de l'affûtage des outils au façonnage et à la finition des composants métalliques. Ils contribuent à la précision et à la qualité des pièces automobiles.
Industrie du bois :
Les menuisiers utilisent des disques abrasifs pour façonner et lisser les surfaces en bois. Ces disques sont efficaces pour éliminer l'excédent de matière, affiner les formes et préparer le bois pour la finition.
Fabrication générale :
Les disques abrasifs trouvent des applications dans divers processus de fabrication où un enlèvement de matière précis est requis, contribuant à la production de composants de haute qualité.
C. Problèmes courants rencontrés
Usure et abrasion du disque :
Une utilisation continue peut entraîner l'usure et l'abrasion du disque de meulage, affectant ainsi ses performances. Une inspection et un remplacement réguliers sont nécessaires pour maintenir son efficacité.
Surchauffe:
Un frottement excessif lors d'une utilisation prolongée peut entraîner une surchauffe, affectant la durabilité du disque et la qualité de sa surface. Un refroidissement adéquat et des pauses régulières sont essentiels.
Colmatage :
Les disques abrasifs peuvent accumuler des résidus, réduisant ainsi leur efficacité. Un nettoyage régulier ou l'utilisation de disques anti-encrassement permet d'éviter ce problème.
Vibration et oscillation :
Des déséquilibres ou une usure inégale peuvent entraîner des vibrations ou des oscillations, affectant la qualité de la finition et la sécurité de fonctionnement. Une installation et un équilibrage corrects sont essentiels.
Sélection de disque incorrecte :
Choisir un disque abrasif inadapté à un matériau ou à une application spécifique peut entraîner une inefficacité et des dommages potentiels. Un choix judicieux, basé sur la compatibilité des matériaux, est essentiel.
Comprendre la définition, l'importance et les défis potentiels des disques abrasifs est essentiel pour les industries qui utilisent ces outils. En abordant les problèmes courants et en garantissant une utilisation appropriée, les industries peuvent optimiser l'efficacité des disques abrasifs dans leurs applications respectives.
Usure des disques de meulage
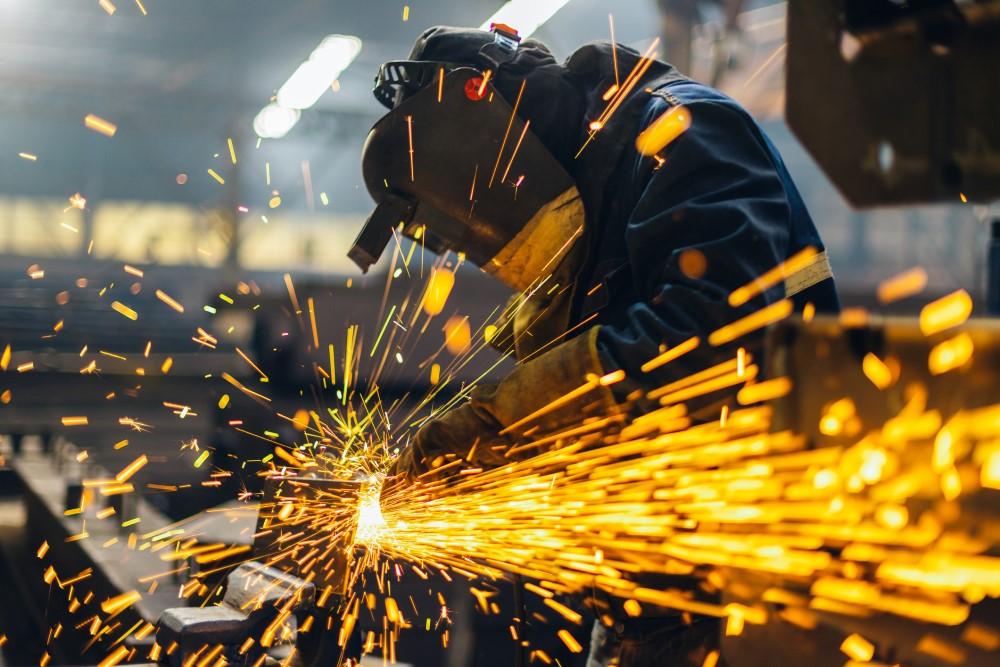
Les disques abrasifs sont des outils essentiels dans de nombreux secteurs, fournissant l'abrasion nécessaire pour des tâches allant de la fabrication de métaux au polissage du béton. Comprendre les facteurs contribuant à l'usure des disques abrasifs est essentiel pour optimiser leurs performances et garantir leur sécurité.
Dureté et composition du matériau :
Variation de dureté :Les disques abrasifs sont utilisés pour traiter des matériaux de dureté variable. La dureté des matériaux abrasifs comme le métal et le béton peut varier considérablement. Le meulage continu sur des matériaux durs accélère l'usure.
Composition du matériau :La présence d'éléments abrasifs dans le matériau à meuler peut impacter l'usure du disque de meulage. Les particules abrasives peuvent accélérer l'usure du disque.
Pression et force de broyage :
Pression excessive :Une pression excessive sur le disque de meulage peut accélérer son usure. Il est essentiel d'utiliser la pression recommandée pour l'application spécifique afin d'éviter toute contrainte inutile sur le disque.
Force insuffisante : En revanche, une force insuffisante peut entraîner un meulage prolongé, générant une friction et une chaleur supplémentaires, contribuant ainsi à l'usure.
Qualité et composition du disque :
Qualité du matériau abrasif :La qualité du matériau abrasif utilisé dans le disque de meulage influence considérablement sa durée de vie. Les matériaux abrasifs de haute qualité ont tendance à résister à l'usure et à conserver leur tranchant plus longtemps.
Agent de liaison :Le liant qui maintient les particules abrasives ensemble joue un rôle crucial. Un liant bien conçu améliore la durabilité du disque.
Conditions de l'environnement de travail :
Température:Les températures élevées générées lors du meulage peuvent affecter la composition du disque. Une chaleur excessive affaiblit le liant et accélère l'usure.
Humidité et contaminants :L'exposition à l'humidité ou aux contaminants dans l'environnement de travail peut affecter l'intégrité du disque de meulage, entraînant une usure plus rapide.
Technique de l'opérateur :
Technique appropriée :Les compétences et la technique de l'opérateur sont essentielles. Une utilisation incorrecte, comme un meulage à des angles incorrects ou une force excessive, peut contribuer à une usure irrégulière et réduire la longévité du disque.
Inspections régulières :Les opérateurs doivent inspecter régulièrement le disque de meulage pour détecter tout signe de dommage ou d'usure. Les disques présentant une usure supérieure à un certain point doivent être remplacés rapidement.
Taille du disque et compatibilité RPM :
Taille correcte :Il est crucial d'utiliser un disque de taille adaptée à la meuleuse. Des disques de taille incorrecte peuvent s'user de manière irrégulière ou présenter des risques pour la sécurité.
Compatibilité RPM :Le respect des tours par minute (RPM) recommandés pour le disque de meulage garantit des performances optimales et évite une usure prématurée.
Un entretien régulier, le respect des conditions d'utilisation recommandées et le choix du disque de meulage adapté à la tâche sont des pratiques essentielles pour minimiser l'usure. En comprenant les facteurs qui influencent l'usure, les opérateurs peuvent améliorer la longévité et l'efficacité des disques de meulage, contribuant ainsi à des opérations de meulage plus sûres et plus productives.
Meulage irrégulier
Le meulage irrégulier se produit lorsque la surface à meuler n'obtient pas une finition uniforme et lisse. Ce problème peut survenir pour diverses raisons et affecter la qualité de la pièce. Voici les facteurs courants contribuant à un meulage irrégulier et les solutions possibles :
Sélection incorrecte de la meule :
Solution:Assurez-vous que la meule est adaptée au matériau à meuler. Chaque matériau requiert des propriétés abrasives spécifiques. Choisissez le type de meule, la granulométrie et le liant adaptés à l'application.
Mauvais dressage des roues :
Cause:Une meule mal affûtée peut entraîner une usure inégale et une coupe inefficace.
Solution:Dressez régulièrement la meule pour conserver sa forme et éliminer les débris accumulés. Un dressage approprié garantit une surface de coupe uniforme.
Liquide de meulage ou liquide de refroidissement inadéquat :
Cause:Une utilisation insuffisante ou inappropriée du liquide de meulage peut entraîner une augmentation de la friction et de la chaleur, conduisant à un meulage inégal.
Solution:Utilisez un liquide de meulage ou de refroidissement approprié pour dissiper la chaleur et réduire les frottements. Un refroidissement adéquat est essentiel pour obtenir des résultats uniformes.
Paramètres de broyage incorrects :
Cause:L'utilisation de paramètres de meulage incorrects tels qu'une vitesse, une vitesse d'avance ou une profondeur de coupe excessives peut entraîner un meulage inégal.
Solution:Ajustez les paramètres de broyage en fonction du matériau et des exigences de l'application. Consultez les recommandations du fabricant pour des réglages optimaux.
Meule usée :
Cause:Une meule usée peut ne pas fournir une surface de coupe uniforme, ce qui entraîne un meulage inégal.
Solution:Remplacez la meule en fin de vie. Inspectez-la régulièrement pour détecter tout signe d'usure.
Pression ou débit d'alimentation inégal :
Cause:Une pression inégale ou des vitesses d'alimentation irrégulières pendant le meulage peuvent entraîner un enlèvement de matière irrégulier.
Solution:Appliquez une pression uniforme et maintenez une vitesse d'avance constante sur toute la pièce. La compétence et le souci du détail de l'opérateur sont essentiels.
Problèmes de machine :
Cause:Des problèmes mécaniques avec la rectifieuse, tels qu'un mauvais alignement ou des problèmes avec la broche, peuvent entraîner un meulage inégal.
Solution:Effectuez des contrôles d'entretien réguliers sur la rectifieuse. Résolvez rapidement tout problème mécanique pour garantir son bon fonctionnement.
Fixation de la pièce :
Cause:Des pièces mal fixées ou mal alignées peuvent entraîner un meulage irrégulier.
Solution:Assurez-vous que la pièce est correctement fixée et alignée. Fixez-la fermement pour éviter tout mouvement pendant le meulage.
La correction des irrégularités de meulage nécessite une configuration adéquate de l'équipement, des paramètres de fonctionnement corrects et des pratiques d'entretien régulières. Les opérateurs doivent être formés pour identifier et corriger rapidement les problèmes afin d'obtenir des résultats de meulage de haute qualité et constants. Des inspections régulières et le respect des meilleures pratiques contribuent à un enlèvement de matière efficace et uniforme pendant le processus de meulage.
Problèmes de surchauffe
La surchauffe pendant le meulage est un problème courant qui peut affecter les performances de la meule et de la pièce. Une chaleur excessive peut entraîner divers problèmes, notamment une réduction de la durée de vie de la meule, des dommages thermiques à la pièce et une diminution générale de l'efficacité du meulage. Voici les causes potentielles et les solutions pour résoudre les problèmes de surchauffe :
Paramètres de broyage incorrects :
Cause:L'utilisation de paramètres de meulage inappropriés, tels qu'une vitesse, une vitesse d'avance ou une profondeur de coupe excessives, peut générer une chaleur excessive.
Solution:Ajustez les paramètres de broyage dans la plage recommandée. Consultez les instructions du fabricant pour connaître les réglages optimaux en fonction du matériau à broyer.
Refroidissement ou lubrification inadéquats :
Cause:Une utilisation insuffisante de liquide de refroidissement ou de liquide de meulage peut entraîner une augmentation des frottements et de la chaleur.
Solution:Assurez un apport suffisant de liquide de refroidissement ou de lubrifiant pendant le processus de rectification. Un refroidissement adéquat permet de dissiper la chaleur et d'éviter les dommages thermiques.
Sélection de roue incorrecte :
Cause:Le choix d'une meule avec des spécifications inappropriées pour le matériau à meuler peut entraîner une surchauffe.
Solution:Choisissez une meule avec le type d'abrasif, la granulométrie et le liant adaptés à l'application. Adaptez la meule au matériau pour minimiser la production de chaleur.
Problèmes liés aux matériaux des pièces :
Cause:Certains matériaux, en particulier ceux ayant une faible conductivité thermique, sont plus sujets à la surchauffe pendant le meulage.
Solution:Ajustez les paramètres de meulage pour les matériaux à faible conductivité thermique. Envisagez d'utiliser une meule spéciale conçue pour les matériaux sensibles à la chaleur.
Problèmes de dressage de roue :
Cause:Des irrégularités ou un dressage incorrect de la meule peuvent entraîner un contact irrégulier et une accumulation de chaleur.
Solution:Dressez régulièrement la meule pour conserver sa forme et éliminer tout glaçage ou débris accumulés. Des meules correctement dressées garantissent des performances de meulage constantes.
Entretien inadéquat de la machine :
Cause:Des rectifieuses mal entretenues peuvent contribuer à des problèmes de surchauffe.
Solution:Effectuez un entretien régulier de la rectifieuse, notamment la vérification des systèmes de refroidissement, l'inspection du matériel de dressage des meules et le bon alignement. Résolvez rapidement tout problème mécanique.
Débit de liquide de refroidissement de roue insuffisant :
Cause:Un débit de liquide de refroidissement insuffisant vers la zone de meulage peut entraîner une dissipation de chaleur réduite.
Solution:Vérifiez et optimisez le système d'alimentation en liquide de refroidissement. Assurez-vous que le liquide de refroidissement atteint efficacement la zone de meulage afin de maintenir l'efficacité du refroidissement.
Temps de broyage excessif :
Cause:Des séances de meulage prolongées sans pause peuvent contribuer à l’accumulation de chaleur.
Solution:Adoptez un meulage intermittent et prévoyez des pauses pour éviter une accumulation excessive de chaleur. Cette approche est particulièrement importante pour les travaux de meulage importants ou complexes.
La résolution des problèmes de surchauffe lors de la rectification nécessite une approche globale impliquant une configuration adéquate de l'équipement, des paramètres de rectification adaptés et des pratiques d'entretien régulières. Les opérateurs doivent surveiller et contrôler la production de chaleur pendant le processus de rectification afin de garantir des performances optimales, une durée de vie prolongée de l'outil et des résultats de haute qualité.
Préoccupations liées aux vibrations
Des vibrations excessives lors des opérations de rectification peuvent entraîner divers problèmes, notamment une dégradation de la qualité de surface, une usure accrue de l'outil et des dommages potentiels à la rectifieuse. Il est essentiel de remédier aux problèmes de vibrations pour obtenir des processus de rectification précis et efficaces. Voici les causes potentielles et les solutions pour atténuer ces problèmes :
Usure inégale des roues :
Cause:Une usure irrégulière de la meule peut entraîner un contact irrégulier avec la pièce, provoquant des vibrations.
Solution:Inspectez et dressez régulièrement la meule pour maintenir une surface plane et uniforme. Un entretien adéquat de la meule permet de minimiser les vibrations.
Meule déséquilibrée :
Cause:Un déséquilibre de la meule, qu'il soit dû à une usure inégale ou à des défauts de fabrication, peut entraîner des vibrations.
Solution:Équilibrez la meule à l'aide d'une équilibreuse. L'équilibrage assure une répartition uniforme du poids et réduit les vibrations pendant le fonctionnement.
Étalonnage inadéquat de la machine :
Cause:Un mauvais calibrage ou un mauvais alignement des composants de la machine, tels que l'axe de la roue ou la table de travail, peut contribuer aux vibrations.
Solution:Calibrez et alignez régulièrement les composants de la machine pour garantir son bon fonctionnement. Suivez les instructions du fabricant pour la configuration et l'alignement de la machine.
Déséquilibre de la pièce :
Cause:Une pièce inégale ou mal fixée peut créer un déséquilibre et induire des vibrations.
Solution:Fixez correctement la pièce en vous assurant qu'elle est positionnée et serrée uniformément. Corrigez tout problème de déséquilibre avant de commencer le meulage.
Sélection de roue incorrecte :
Cause:L’utilisation d’une meule avec des spécifications inappropriées peut entraîner des vibrations.
Solution:Choisissez une meule avec le type d'abrasif, la granulométrie et le liant adaptés au matériau à meuler. Adaptez la meule à l'application pour minimiser les vibrations.
Usure de la machine :
Cause:Les composants de la machine usés ou endommagés, tels que les roulements ou les broches, peuvent contribuer aux vibrations.
Solution:Inspectez et remplacez régulièrement les pièces usées de la machine. Un entretien approprié permet d'éviter les vibrations excessives et de prolonger la durée de vie de la rectifieuse.
Débit de liquide de refroidissement insuffisant :
Cause:Un débit de liquide de refroidissement insuffisant vers la zone de meulage peut entraîner une accumulation de chaleur et des vibrations.
Solution:Optimisez le système d'alimentation en liquide de refroidissement pour assurer un refroidissement adéquat. Un refroidissement efficace réduit les risques de dilatation et de contraction thermiques, sources de vibrations.
Problèmes liés au porte-outil :
Cause:Des problèmes avec le porte-outil ou l'interface de la broche peuvent introduire des vibrations.
Solution:Assurez-vous que le porte-outil est solidement fixé et correctement aligné avec la broche. Utilisez des porte-outils de qualité et bien entretenus pour minimiser les vibrations.
Fondation de la machine :
Cause:Une mauvaise fondation de la machine ou un support inadéquat peuvent amplifier les vibrations.
Solution:Assurez-vous que la rectifieuse est installée sur une fondation stable et correctement conçue. Corrigez tout problème structurel afin de minimiser les vibrations transmises à la machine.
Pour gérer efficacement les problèmes de vibrations lors de la rectification, il est essentiel de combiner un entretien adéquat de la machine, le choix de la meule et la manipulation des pièces. Les opérateurs doivent mettre en œuvre des pratiques d'inspection et de maintenance régulières afin d'identifier et de résoudre rapidement les problèmes, améliorant ainsi les performances et la qualité de la rectification.
Problèmes de chargement lors du broyage
L'encrassement lors de la rectification se produit lorsque les espaces entre les grains abrasifs de la meule se remplissent de matière à rectifier, ce qui réduit l'efficacité de coupe et augmente la friction. L'encrassement peut nuire à l'efficacité et à la qualité du processus de rectification. Voici quelques causes et solutions potentielles pour résoudre ce problème :
Matériau de la pièce souple :
Cause:Le meulage de matériaux tendres peut entraîner un colmatage rapide des grains abrasifs.
Solution:Pour travailler sur des matériaux tendres, utilisez une meule à gros grains et à structure ouverte. Cela permet d'éviter un encrassement rapide et d'évacuer efficacement les copeaux.
Contamination matérielle :
Cause:Les contaminants présents dans le matériau de la pièce, tels que les huiles, la graisse ou les résidus de liquide de refroidissement, peuvent contribuer à la charge.
Solution:Assurez-vous de bien nettoyer la pièce avant le meulage afin d'éliminer les contaminants. Utilisez des liquides de coupe ou de refroidissement appropriés pour minimiser l'encrassement.
Application incorrecte du liquide de refroidissement :
Cause:Une application inadéquate ou incorrecte du liquide de refroidissement peut entraîner une lubrification et un refroidissement insuffisants, entraînant une surcharge.
Solution:Optimiser le débit et la concentration du liquide de refroidissement. S'assurer que le liquide de refroidissement atteint efficacement la zone de meulage pour lubrifier et refroidir le processus, évitant ainsi tout encrassement.
Netteté insuffisante de la roue :
Cause:Les meules émoussées ou usées sont plus sujettes à l'encrassement car elles perdent leur efficacité de coupe.
Solution:Dressez et affûtez régulièrement la meule pour conserver son tranchant. Utilisez un dresseur de meule pour exposer les grains abrasifs frais et améliorer la coupe.
Faible vitesse de roue :
Cause:L'utilisation de la meule à faible vitesse peut ne pas fournir suffisamment de force centrifuge pour éjecter les copeaux, ce qui peut entraîner un encrassement.
Solution:Assurez-vous que la rectifieuse fonctionne à la vitesse recommandée pour la combinaison meule-pièce. Des vitesses plus élevées permettent une meilleure évacuation des copeaux.
Pression excessive :
Cause:Appliquer trop de pression pendant le meulage peut forcer le matériau à pénétrer dans la meule, provoquant ainsi un encrassement.
Solution:Appliquez une pression de meulage modérée et constante. Réglez la vitesse d'avance pour permettre à la meule de couper efficacement sans pression excessive susceptible d'entraîner un encrassement.
Spécifications de roue incorrectes :
Cause:L'utilisation d'une meule avec des spécifications incorrectes pour le matériau à meuler peut entraîner une surcharge.
Solution:Choisissez une meule avec le type d'abrasif, la granulométrie et le liant adaptés à l'application. Adaptez la meule au matériau afin d'éviter l'encrassement.
Nettoyage inadéquat du liquide de refroidissement :
Cause:Un liquide de refroidissement contaminé ou ancien peut contribuer à des problèmes de chargement.
Solution:Nettoyez et remplacez régulièrement le liquide de refroidissement pour éviter l'accumulation de contaminants. Un liquide de refroidissement frais et propre améliore la lubrification et le refroidissement, réduisant ainsi le risque de formation de dépôts.
Mauvaise technique d'habillage :
Cause:Un dressage incorrect de la meule peut entraîner des irrégularités et des charges.
Solution:Dresser correctement la roue à l'aide de l'outil de dressage approprié. S'assurer que le profil de la roue est uniforme et exempt d'irrégularités afin d'éviter toute surcharge.
La résolution efficace des problèmes de charge implique une combinaison de choix de meule, de configuration de la machine et de pratiques d'entretien appropriées. Les opérateurs doivent suivre les procédures recommandées, utiliser des paramètres de meulage adaptés et effectuer un dressage régulier de la meule afin de minimiser la charge et d'optimiser les performances de meulage.
Choisir le bon disque de meulage est crucial pour obtenir des résultats optimaux dans diverses applications de travail des métaux et de fabrication. Le choix dépend de facteurs tels que le matériau travaillé, la finition souhaitée et le type de meuleuse utilisée.
Choisir le bon disque de meulage
Compatibilité des matériaux :
Métaux ferreux (acier, fer) :Utilisez des disques abrasifs spécialement conçus pour les métaux ferreux. Ces disques contiennent souvent des abrasifs adaptés à la dureté de l'acier et sont moins sujets à l'encrassement.
Métaux non ferreux (aluminium, laiton) :Choisissez des disques abrasifs adaptés aux métaux tendres pour éviter l'encrassement. Les disques en oxyde d'aluminium ou en carbure de silicium sont des choix courants.
Matériau abrasif :
Oxyde d'aluminium :Convient au meulage général des métaux ferreux. Durable et polyvalent.
Zircone Alumine :Offre une efficacité de coupe et une longévité supérieures, ce qui le rend adapté au meulage agressif des métaux ferreux et non ferreux.
Carbure de silicium :Idéal pour le meulage des métaux non ferreux et de la pierre. Il est plus tranchant, mais moins durable que l'oxyde d'aluminium.
Taille du grain :
Gros grain (24-36) :Enlèvement rapide de matière et meulage intensif.
Grain moyen (40-60) :Équilibre l'enlèvement de matière et la finition de surface.
Grain fin (80-120) :Offre une finition lisse, adaptée à la préparation de surface et au meulage léger.
Type de roue :
Type 27 (centre déprimé) :Disque de meulage standard avec surface plane, idéal pour le meulage de surface et le travail des bords.
Type 29 (conique) :Conception inclinée pour un retrait agressif des matières et un meilleur mélange de surface.
Type 1 (droit) :Utilisé pour les applications de tronçonnage. Son profil fin assure une coupe précise.
Application:
Affûtage:Disques de meulage standard pour l'enlèvement de matière et le façonnage.
Coupe:Utilisez des disques à tronçonner pour couper le métal, en obtenant un bord droit et propre.
Disques à lamelles :Meulage et finition combinés. Convient pour le lissage et le ponçage des surfaces.
Compatibilité avec Grinder :
Assurez-vous que le disque de meulage est compatible avec le type et la vitesse de la meuleuse utilisée. Consultez les recommandations du fabricant concernant le régime maximal du disque.
Spécificité de la tâche :
Enlèvement de matières importantes :Choisissez un grain grossier et un disque de type 27 ou de type 29 pour une élimination efficace de la matière.
Finition de surface :Optez pour des grains moyens à fins avec des disques à lamelles pour des finitions plus lisses.
Considérations de sécurité :
Suivez les consignes de sécurité, notamment en portant un équipement de protection individuelle (EPI) approprié, tel que des lunettes de sécurité et des gants.
Choisissez des disques renforcés pour plus de durabilité et de sécurité.
Marque et qualité :
Choisissez des disques de marques réputées, reconnues pour leur qualité et leur régularité. Les disques de haute qualité offrent de meilleures performances et une meilleure durabilité.
Considération des coûts :
Équilibrez le coût initial avec la durée de vie et les performances attendues du disque abrasif. Les disques de haute qualité peuvent être plus coûteux à l'achat, mais offrent un meilleur rapport qualité-prix à long terme.
En tenant compte de ces facteurs, les opérateurs peuvent choisir le disque de meulage adapté à leurs applications spécifiques, garantissant ainsi efficacité, sécurité et résultats optimaux.
Conclusion
En conclusion, le choix du disque de meulage approprié est essentiel pour obtenir de bons résultats en matière de travail des métaux et de fabrication. Le choix dépend de divers facteurs, tels que le matériau travaillé, la finition souhaitée et le type de meuleuse utilisé. En tenant compte de la compatibilité des matériaux, du type d'abrasif, de la granulométrie, du type de meule, de l'application, de la compatibilité avec la meuleuse, de la spécificité de la tâche, de la sécurité, de la qualité de la marque et du coût, les opérateurs peuvent prendre des décisions éclairées pour améliorer l'efficacité et la sécurité de leurs processus de meulage.
Il est essentiel de respecter les consignes de sécurité, de porter un équipement de protection individuelle approprié et de suivre les recommandations du fabricant concernant la compatibilité de la meuleuse et du disque. Qu'il s'agisse d'enlèvement de matière important, de finition de surface ou de coupe, le choix d'un disque de meulage adapté peut avoir un impact significatif sur la qualité et l'efficacité du travail.
De plus, des contrôles périodiques de l'usure, la résolution des problèmes tels que la surchauffe et les vibrations, et la compréhension des problèmes de chargement contribuent à prolonger la durée de vie du disque de meulage et à garantir des performances constantes.
En résumé, une approche bien informée et systématique de la sélection, de l’utilisation et de l’entretien des disques de meulage est essentielle pour obtenir des résultats optimaux, améliorer la productivité et garantir un environnement de travail sûr.
Date de publication : 12 janvier 2024